Achieving Cnesst Compliance: Key Tips For Warehousing Success
Table of ContentsThe Anatomy Of A Successful Warehouse Compliance Inspection7 Warehouse Inspections You Need To Carry OutPalettier Cnesst: How To Stay Up-to-date With Changing RegulationsThe Importance Of Racking Maintenance In Warehouse OperationsCreating A Culture Of Warehouse Safety In CanadaThe Evolution Of Warehouse Safety In Canada
Do not operate devices. Ask the operator for a demo. If the operator of any item of devices does not recognize what risks may be present, this fact is reason for issue. Never overlook any kind of thing since you do not feel you have the knowledge to make an accurate judgement of security.Do not spoil the examination with a "once-over-lightly" approach. Tape-record what you have or have not taken a look at in case the evaluation is interrupted. Ask inquiries, but do not needlessly interrupt work tasks.
The Evolution Of Warehouse Safety In Canada
Consider the fixed (stop placement) as well as vibrant (in motion) problems of the item you are examining. If a device is closed down, take into consideration holding off the inspection till it is functioning again. Take into consideration elements such as exactly how the job is arranged or the rate of work and also just how these aspects effect safety and security - Inspection de conformite.
"How serious are the prospective outcomes?" "Do any type of safety policies use?". Determine what corrections or controls are appropriate. Securite des entrepots. Do not try to find all threats merely by counting on your senses or by checking out them throughout the evaluation. You may have to demand that devices is kept track of to measure the degrees of exposure to chemicals, noise, radiation, or organic representatives.
Addressing The Top Causes Of Accidents In Warehouse Safety
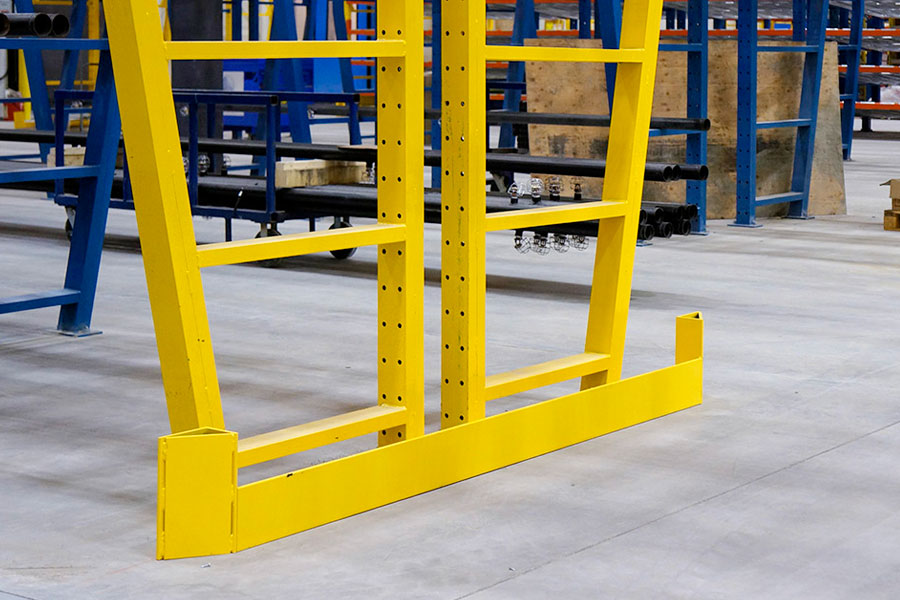
State specifically what has actually been spotted as well as properly determine its location. A person who was not present ought to be able to locate the exact same product based on the info given.
Racking Safety: Mitigating The Risk Of Human Error
See to it that photos are linked to the correct products. Now that the observed things have been noted, they can be further identified and reviewed. Assign a danger classification per detailed product according to the picked plan (e. g., electrical, material handling, maker protecting, ergonomic, organic, psychosocial, and so on). Keep go to this site in mind if the product is a repeating safety and security issue.
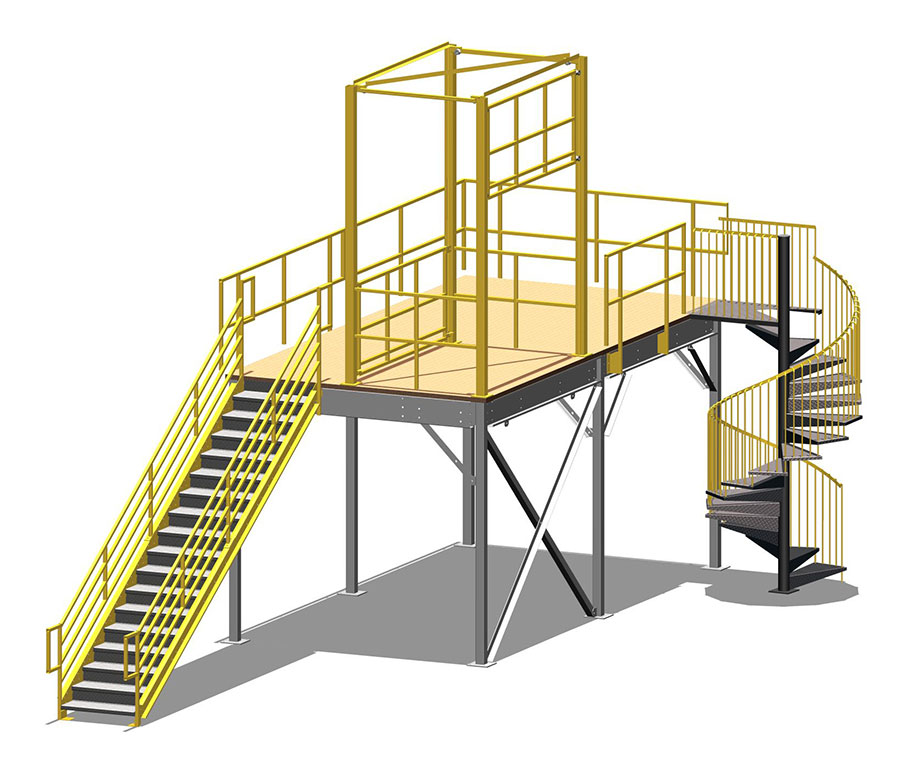
Racking Maintenance Tips For Busy Warehouse Managers
Risks that score high in both will have the best top priority. After each listed item, define the advised rehabilitative action (e. g., control methods , repair order, items to acquire, training, and so on). Assign a responsible individual and establish a certain modification due day ideally as well as ideal. One detailed risk might call for numerous restorative actions.
g., open, on hold, closed, and so on). Because some corrective activities might take longer to complete, consider copying all unfinished things from the previous report onto the new report (include their special ID numbers). The final record may be composed by a single assigned person who obtains the examination notes, or by the assessment group with each other throughout a post-inspection meeting.
Cnesst Compliance: Understanding The Penalties And Consequences
Report issues as well as suggestions in a concise, accurate method. Monitoring should be able to understand as well as assess the troubles, appoint priorities, and swiftly get to decisions. Conformite CNESST. Review the information from normal inspections to identify where restorative activity was required. Figure out if these activities have actually been taken. Usage older reports to determine trends.
This evaluation can be made use of as part of the continual renovation process for the occupational wellness as well as safety and security program or management system. Number 1: Example of a flooring representation Reality sheet last revised: 2022-10-26.